The Hidden Solution to Importers’ “Inventory Glut” Problem
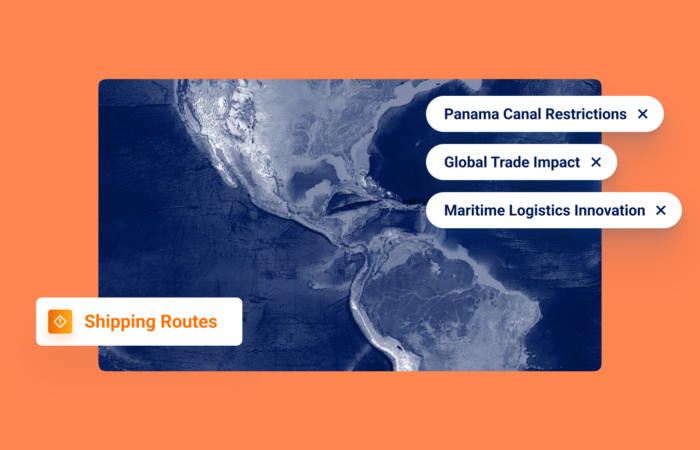
What’s inside?
“Excess inventory is a $250+ billion problem in the U.S. alone, according to a 2023 Kearney study. On a global scale, U.S. census data shows excess inventory amounts to trillions of dollars. Someone pays for all that extra inventory.
And this problem isn’t a pandemic-era anomaly. New demand spikes are coming our way – you only have to consider the seemingly ‘infinite’ demand for electric vehicle batteries or the boom of chipsets that drive AI-powered technology to see how similar cycles could play out in the near future.”
This analysis from a recent article in Harvard Business Review squares with what Windward is hearing from customers and seeing across industries.
Windward’s suggested approach involves obtaining the confidence that results from actionable visibility. With a full picture of your ocean freight operations and the ability to proactively handle exceptions, you can manage your inventory and supply chain much more effectively.
Safety Stock Endangers Your Bottom Line
The reduction of safety stock has a direct impact on working capital and cash flow. Cutting costs becomes especially critical during recessions and inflationary periods, emphasizing the need for vigilant safety stock management to safeguard the bottom line.
For importers and manufacturers that manage large-volume operations, maintaining high “just in case” stocks is problematic on multiple levels. Excess inventory from carrying too much safety stock can lead to expired goods; waste; and elevated warehousing, rent and handling expenses.
Plus, the tied-up capital elevates insurance fees and limits funds for other revenue-generating activities.
Critical Event Management’s Exceptional Results
Critical events management is about pinpointing, considering, and addressing disruptions within the shipping process. These critical events can involve a range of issues that affect delivery schedules, including port congestion and route issues, both of which can disrupt the supply chain.
When we think about managing critical supply chain events and effects on costs, we often associate savings with avoiding fees. By managing supply chain exceptions proactively, businesses can reduce demurrage fees, detention costs, and other penalties related to non-compliance, or inefficient operations.
A data analysis of 1,300 containers proves that companies can also optimize their safety stock more effectively with Windward’s critical events management insights, to reduce related costs.
Based on Windward’s empirical data and research, stock levels are typically monitored 25 days prior to containers actual time of arrival, but they can also be modified after the 25-day period begins. This 25-day window is a crucial threshold, as decisions regarding orders are usually made within this time frame. Below are three Windward proactive insights categories that enable decisions to be made quickly, after or up to seven days before the 25-day threshold:
- Late departure from POL: when notified within 20 days before arrival at the port of destination, Windward’s critical event management insights helped manufacturers know that their containers will be delayed by 7 days
- This helped organizations calculate safety stocks at destination
- Rollover at POL/TSP: when notified within 22 days before arrival at the port of destination, Windward’s insights helped our customers predict a nine-day delay
- This makes is possible to reduce incoming materials from other suppliers, or dispose of excess and obsolete inventory items to save warehouse space
- Transshipment delay: when notified within 32 days before the port of destination, Windward’s insights helped customers know in advance that there will be a delay of 22 days
It is possible to expedite alternative freight with additional costs (air freight, for example).
Solving a Critical Problem
The HBR article noted that, “Inventory management is a critical problem that should be on the radar of anyone in an industry with volatile demand and long lead times. And it requires a careful, collective solution. No single company stands alone. Instead, we’d all be well served to consider the broader business ecosystem, making decisions that will serve our bottom lines and the health of all the companies connected to us.”
Well-said. We have one relatively straight-forward solution.
Organizations with extensive inventories worldwide often face significant inventory costs. By implementing Windward exception management, even a modest reduction of safety stock by just 2 percent could result in substantial savings in a short period of just a few months.