Navigating Transshipment Challenges
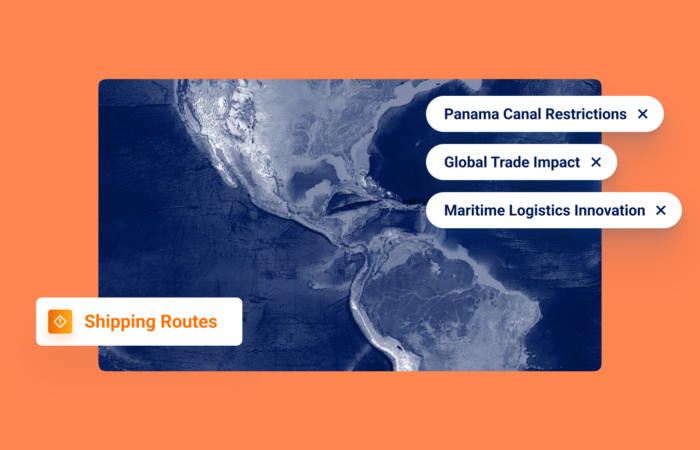
What’s inside?
Shipping delays resulting from transshipment entanglements can have significant implications for businesses operating in the maritime industry. These delays disrupt supply chain operations, impact customer satisfaction, and increase costs. By understanding the common causes of transshipment delays and implementing effective strategies to overcome them, businesses can navigate ocean transshipment challenges more efficiently.
In this blog post, we’ll explore the various reasons that contribute to transshipment and shipping delays in ocean transshipments and explain how a Maritime AI™ solution can help.
Why are Transshipments Common?
Transshipments are a common occurrence in the ocean leg of the supply chain. Here are a few reasons why:
- No direct link between locations: transshipments arise when there is no direct or economically viable route connecting the port of origin to the port of destination. In such instances, containers must undergo transfers between vessels to reach the final location efficiently.
- Port of destination not available: when the port of destination is not available because of low tide, weather, or if it cannot accommodate mega-vessels, the containers are transferred to a different/smaller vessel to arrive at the destination port.
- Reduced costs: direct shipping is usually costly, transshipments may take longer but are often a cheaper option.
The Importance of Container Tracking and Transshipments
As mentioned in our container tracking guide, “…transshipment scenarios complicate the issue, often forcing shippers and freight forwarders to act as detectives to try and figure out exactly where their container is and where it’s going. In more complex scenarios, there could even be more than one intermediate port along the way…It’s important to differentiate between container and vessel journeys. Multiple vessels may carry one container on its journey from the original port of loading (POL) to the POD. For example, container X will leave its POL on vessel A, stop at a transshipment port or hub, and be transferred to vessel B and from there to the POD.”
These complex scenarios can easily cause confusion, but with a solution that provides intuitive container tracking and exception management, it is manageable.
With exception management, you can simply filter shipments and identify those that are significantly or critically late, or early. Armed with this information, you can take appropriate action to mitigate any potential issues. This results in improved efficiency, freeing up personnel to concentrate on their core responsibilities.
The Complexity of Transshipments
Transshipment is a complex supply chain challenge that involves the transportation of cargo or a container from one vessel to another while in transit to its final port of discharge (POD).
Transshipments mostly occur when cargo cannot reach its final destination via a direct route. One of the main reasons for delays is transshipment delays. Delays result when it takes longer than initially scheduled for cargo to be transferred from one vessel to another.
Another reason for delay is a short transshipment buffer that occurs when there is limited time allocated for transshipment operations. A small transshipment window increases the risk of disruptions and can lead to further shipment delays. According to Windward’s research, 25% of delayed shipments are caused by complications during a transshipment.
Transshipment delays can occur due to various complications, such as logistical issues, mechanical failures, or insufficient port resources. As explained by SeaRates, containers can also be delayed if there is an identification of violations that may lead to the apprehension of containers or even a vessel. Usually there are various customs posts that the container will pass, and in the case of transshipment ports, there are even more of them. At the same time, customs authorities at the port of transshipment can also assign control actions to your cargo, and even in this case they can be delayed.
Weather conditions can also effect delays, with strong winds, tropical storms and typhoons causing serious problems at the transshipment complex. Port or terminal congestion usually happens when the number of containers arriving at the port exceeds the norm. This specifically applies to transshipment ports, where the turnover of transit cargoes is much higher than import-export. The vessel needs to wait longer for the start of cargo operations until the work on the previous cargoes is completed.
Other Shipping Delays: Late Departures, Rollovers, & Unfeasible Journeys
Of course, there are delays beyond transshipments. Late departures, where vessels leave the POL behind schedule, also contribute to shipping delays in the ocean leg of the supply chain. Mechanical issues, documentation errors, or unforeseen circumstances at the port can cause vessels to depart later than planned. Late departures create a domino effect throughout the supply chain, resulting in the delayed arrival at the transshipment port, and eventually at the POD.
Another reason for shipping delays in the supply chain is rollovers, where containers scheduled to be loaded onto a specific vessel fail to make it onto that vessel at the POL or the transshipment port. Rollovers disrupt the expected flow of goods, leading to shipping delays and potentially affecting the ETA for delivery. Unfeasible journeys also pose challenges and occur when carrier-provided transit time estimations are too short, based on available data and estimations.
Maritime AI™ Can Help
To address these various challenges, leveraging technology solutions that provide real-time, actionable visibility throughout the supply chain is a must. With a Maritime AI™ platform, this is possible. Maritime insights into the various reasons for delays, specifically those connected to transshipments, can empower you to make more informed decisions. They also ensure efficient planning to avoid late fees and penalties, such as detention and demurrage charges.
Streamlining operations, optimizing transshipment windows, and ensuring realistic transit time estimations can minimize shipping delays and provide reliable and efficient services, meeting customer expectations for timely delivery. The power of actionable visibility lies in its ability to transform your business processes and provide clarity and value to your internal operations, employees, and customers.